当前位置:
天津 恒永兴金属材料销售
有限公司 >扬州本地行业热点
【铝合金型材,结构管厂家批发价】
更新时间:2025-03-16 22:28:51 浏览次数:15 公司名称:天津 恒永兴金属材料销售 有限公司
以下是:【铝合金型材,结构管厂家批发价】的产品参数
产品参数 | |
---|---|
产品价格 | 344 |
发货期限 | 电议 |
供货总量 | 电议 |
运费说明 | 电议 |
品牌 | 恒永兴 |
规格 | 齐全 |
价格 | 电议 |
以下是:【铝合金型材,结构管厂家批发价】的图文视频
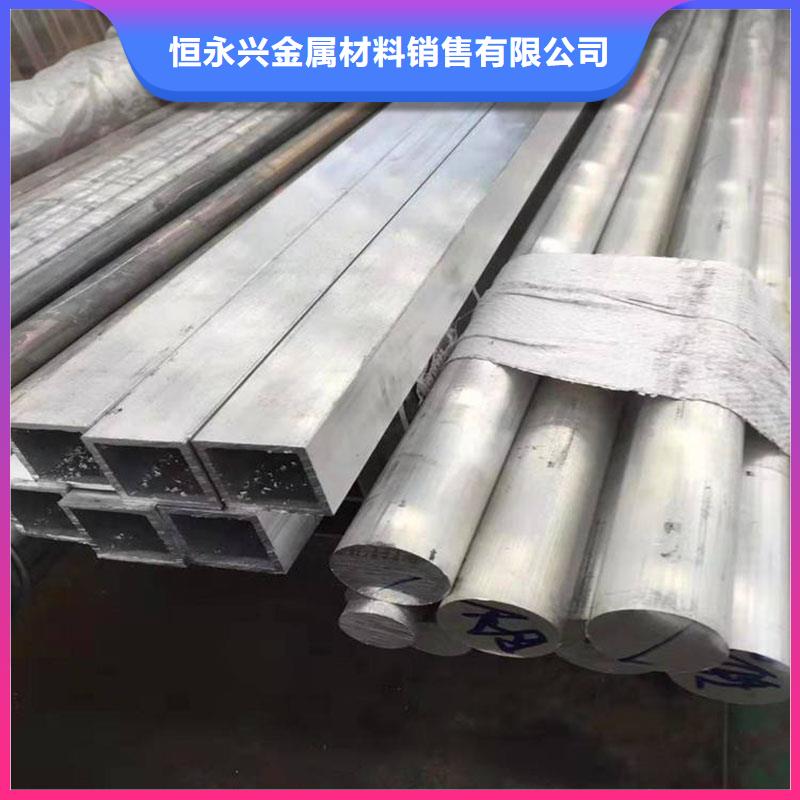

【铝合金型材,结构管厂家批发价】,恒永兴金属材料销售
有限公司专业从事【铝合金型材,结构管厂家批发价】,联系人:李经理,电话:022-86869388、18802286588,QQ:554918566,发货地:天津北辰区双街镇京津路西(北方实业发展有限公司内)发货到江苏省 扬州市 广陵区、邗江区、江都区、宝应县、仪征市、高邮市,以下是【铝合金型材,结构管厂家批发价】的详细页面。 江苏省,扬州市 扬州市历史悠久,是全国首批24座历史文化名城之一。自吴夫差十年(前486年),吴王夫差开邗沟、筑邗城始,已有2500多年建城史。扬州市是南京都市圈紧密圈城市和长三角城市群城市,重点工程南水北调东线水源地。有着“淮左名都,竹西佳处”之称;又有着“中国运河城”的美誉。在中国历史上,扬州因其独特的地理位置和优越的自然环境,自汉代至清代几乎经历了通史式的繁荣,并伴随着文化的兴盛。中国大运河扬州段入选世界遗产名录;扬州列入中国海上丝绸之路。
简约不浮华,不简单实用。我们的【铝合金型材,结构管厂家批发价】产品视频用直观的方式展现产品的实用性和价值。
以下是:【铝合金型材,结构管厂家批发价】的图文介绍
恒永兴金属材料销售 有限公司是集 江苏扬州工字钢生产加工经营于一体的大型企业,公司成立至今一直秉承以用户需求为核心,在专注市场开拓的同时,为客户提供产品与服务,用心的服务赢得了众多客户的信赖和好评,在周边地区逐渐树立起公司良好品牌。 公司将不断完善并研发产品质量的理念精神。年轻队伍,以实际行动为客户提供更好的服务,以精挑细琢的姿态为客户创造性价比产品。 公司愿景:万分的努力,只为能给客户赢得十分的满意!我们相信,通过我们的不断努力和追求,一定能够实现与您互利共赢!
1.夹具的设计与制作:1.1夹具的特点:铝件加工后阳极氧化用的夹具与电镀用的挂具是截然不同的,若采用电镀用类似挂勾的挂具作阳极化夹具是不适宜的,因为阳极氧化时夹具与工件表面都会很快生成氧化膜,在此过程中夹具与工件稍有松动即会变更触点位置,阻碍电流流通,为此,必须采用具有弹性的夹具夹紧工件。只有这样才能使阳极氧化过程正常进行。1.2夹具的结构形式:夹具结构以个体式为宜,若采用组装式的,则经几次使用后铆接或焊接处会因腐蚀而松动,阻碍阳极氧化过程中电流的正常流通。同时,夹具要有一定的横截面积。一定截面的夹具也就有足够的弹力和夹紧力,使工件与夹具保持良好的接触,保证所夹工件阳极氧化时所需电流正常流通。避免因接触不良产生热量而烧毁工件。1.3夹具材料的选择:制作夹具以选择硬质铝材为好,硬质铝材弹性好,紧固耐用。2.工件的装夹:2.1给夹具清洗去膜:在阳极氧化过程中夹具也会产生氧化膜。为此,使用过的夹具再次使用之前一定要退除氧化膜。退膜可在铝的除油溶液中进行。也可将夹具与工件接触部位的氧化膜用锉刀锉去,此法对某些夹具来说还可延长夹具的使用寿命。2.2装夹位置的选择:装夹工件的位置要选择得当,铝合金加工厂一般应装夹在工件的副面(即非装饰的部位)。否则工件与夹具的接触部位因被夹具遮盖而无法生成氧化膜,当然也就无法染上颜色,此处即会显现出明显的白色斑点,影响外观质量。此外,工件装夹后悬挂在溶液中的凹入部位会否产生窝气等问题也要予以考虑。2.3防止工件装夹变形:夹具非同挂具,夹具有一定的弹性。装夹变形的工件时尤需注意,应避免用力过猛导致工件变形。2.4防止装夹过松:当工件装夹过松时,夹具与工件之间的电流会时通时断,在这种情况下很可能把工件烧毁。2.5逐一装夹需染色的阳极化件:有些单位对某些小件采用纱窗布包扎或用其它方法包扎后作阳极氧化处理。这种方法虽在一定场合下可节省工时和提率,但只可用于某些质量要求不高的本色阳极氧化,即使少量工件在相互遮盖处无法生成氧化膜,也不易被识别出来。但对于需要染黑色的工件,采用此种装夹方法显然是不可取的。必须逐一装夹,保证阳极氧化质量。3.精密铝合金零件加工阳极氧化工艺条件的控制:3.1溶液的温度与电压的关系:在额定的范围内溶液的温度越低,所需的电压应越高,因为溶液温度较低时氧化膜生成速度较缓慢,膜层较为致密,为获得一定厚度的氧化膜,阳极氧化过程需升高电压。当溶液的温度较高时,氧化膜的溶解速度加块,且生成的氧化膜是疏松的,此时降低电压能适当改善氧化膜的质量。3.2阳极氧化溶液的温度与时间的关系:溶液的温度越低,所需的阳极氧化时间应越长。因为溶液温度较低时氧化膜的生成速度缓慢。溶液的温度升高时则氧化膜的生成速度加快。此时要缩短阳极氧化时间,否则由于氧化膜的外层电阻加大而导致膜层溶解,出现工件尺寸的改变、表面粗糙掉膜的现象。
铝型材散热器生产工艺:首先贴膜不能直接贴在铬化层上,否则会影响膜的附着力;其次,贴膜后要及时喷涂不能停放时间过长,否则容易导致贴膜脱落,严重时还要重新贴膜;再次是撕膜时要控制流平时间,不能贴膜后马上撕膜,这样会对产品质量带来一定的影响;*后是两种颜色的喷涂顺序要根据具体情况确定,既要考虑到两次固化,又要考虑到遮盖效果。贴膜质量控制:散热器铝型材质量控制中贴膜质量很重要,若贴不好,会导致喷涂困难,如贴膜的张力不大、压紧程度要控制好;对形状复杂的部位要分开贴膜,贴膜后要检查贴膜是否贴牢。否则将会给喷涂带来麻烦。影响喷涂质量。公司生产的铝型材产品均由专业的技术人员严格把关,并拥有专业的生产设备,保证质量问题,客户可放心选购我厂产品。铝型材散热器的贴膜材质:首先要对贴膜材质合理选择,根据散热器铝型材产品的要求、表面处理方式,选择相应的贴膜,同是还要考虑贴膜上的胶对铝型材表面质量的影响。
缩孔是铝合金压铸件常见的内部缺陷,常出现在产品壁厚较大或者易形成热点的位置。一般来讲,只要缩孔不影响产品的使用性能,都以合格的方式来判定。然而,对于一些重要部位,如汽车发动机汽缸体的冷却水道孔或润滑油道孔,出现缩孔是不允许判定合格的。
某企业的一款铝合金制发动机曲轴箱,采用布勒28000kN冷室压铸机铸造,材质为ADC12合金,成分见表1。铸件毛坯质量为6.3 kg,后工序进行X射线探伤时发现第二个曲轴轴承孔油道出现缩孔,离油道约8 mm,存在较大的漏油风险。据统计,2017年该位置的缩孔报废率为5%,经过一系列的探索,成功地将废品率降低为0.2%。本课题从铝合金压铸件缩孔的形成机理[1-5]和铸造条件两方面出发,分析铸件产生缩孔的原因,寻求改善措施,以期为日后解决铝合金压铸件缩孔问题提供参考。一、铝合金压铸件缩孔形成机理及形态--缩孔形成机理:导致铝合金压铸件缩孔的原因较多,追溯其本源,主要是铝合金从液相向固相转变过程中铝液补缩不足而导致。常见的缩孔原因有:①模温梯度不合理,导致铝液局部收缩不一致。②铝液浇注量偏少,导致料饼薄,增压阶段补压不足。③模具存在热结或尖锐区域。④模具的内浇口宽度不够,面积较小,导致铸件过早凝固,增压阶段压力传递受阻、铝液无法补缩。⑤铸造压力设置过低,补缩效果较差。图1为铝合金铸件缩孔形成的示意图。铸件缩孔形态:缩孔是一种铝合金压铸件乃至铸件常见的内部缺陷,常出现在产品壁厚较大、模具尖角和模温温差较大等区域。图2为某款发动机曲轴箱缩孔形态,缩孔呈似椭圆状,距离轴承油道孔约10 mm,内壁粗糙,无光泽。缩孔区域铸件壁厚较大,约为22 mm;油道孔销子前端无冷却水,模温较高。汽车发动机曲轴的两大轴颈(主轴颈和连杆轴颈)工作载荷较大,磨损严重,工作时必须进行压力润滑。在此情况下,轴颈的油道孔附近若存在缩孔,将会严重影响润滑效果。二、缩孔相关对策:铝合金压铸件产生铸造缺陷的原因有产品本身的结构特征、模具设计得浇注系统及冷却系统设计不合理、工艺参数设计不合理等原因[1~4]。根据常见的铸造缺陷原因以及铝合金铸件缺陷处理流程,探索解决铝合金压铸件厚大部位缩孔的相应对策。前期分析及对策:铸件缩孔的前期分析从容易操作的工艺参数出发,通过现场测量及观察,测得模具内浇口厚度为4 mm,计算的内浇口速度为40 m/s,产品壁厚*薄处为4.6 mm;料饼厚度为25 mm;铸造压力为60MPa。由经验可知,模具设计符合产品的结构特征,模具浇注系统应该不存在增压阶段补缩不足的问题。但是,增压阶段的铝液补缩与料饼厚度和增压压力有直接的关系,合适的料饼厚度与铸造压力才能形成内部组 织致密的铸件,因此,可以怀疑缩孔是由铸造压力偏低和料饼偏薄而导致的。前期铸件缩孔的对策分为两个:①铸造压力由之前的65MPa提高至90MPa;②料饼厚度有原来的25 mm调整为30 mm。采用上述措施后,经过小批量专流验证,缩孔率由5%减低为4.8%,效果不明显,说明工艺参数不是引起铸件缩孔的主因。中期分析及对策:由于引起铸件缩孔的本质原因是铝液凝固时补缩不足而导致,而模具温度分布不均容易导致铝液凝固顺序不合理,从而补缩不足,因此,中期对策分析主要从确保合理的模具温度入手。由产品3D模型可知,铸件缩孔处壁厚为22.6mm,壁厚较大,容易引起较高的模具温度。铝液凝固时,壁厚较大铸件内部铝液由于温度较高,尚处于液相或者固液混合相,而此时内浇口进行补缩的通道可能已经凝固。这样,在增压阶段铸件无法进行铝液补缩,从而有形成缩孔的可能。为确保合适的模具温度,采用热成像仪测得脱模剂喷涂后模具*高温度为272℃(见图3),高于正常的模具喷涂后温度,其他区域模具温度及其分布整体正常。因此,需要降低缩孔处模温。另外,测得此处冷却水孔底部距离模具型腔表面距离较大为20 mm,因为较大的热传递距离会降低模具的冷却效果,所以需要对冷却水孔进行更改。为降低缩孔处模具温度,主要采取3个方法:①改善模具冷却系统。将缩孔附件的冷却水孔深度加深,由距模具表面20 mm变成12 mm,以此快速带走附近模具热量,降低模温;将所有模具冷却水管与水管统一编号,一一对应,防止模具保全时装错,影响冷却效果[5,6]。②降低浇注温度,由675℃变为645℃。③延长缩孔处模具喷涂时间,由2 s变成3 s。实施上述整改措施后,缩孔区域模具喷涂后温度大幅度降低,约为200℃,属于正常范围。缩孔率有4.8%降低到4%,说明此类措施对缩孔具有一定效果,但不能彻底解决此区域的缩孔问题。后期分析及对策:通过前面两次改善,基本保证压铸模具处于理论上的合理状态,即浇注系统设计合理、冷却系统布置合适,工艺参数设计*优。然而,铸件缩孔率仍有4%之多。铸件缩孔处壁厚为22.6 mm,远大于其他部位的壁厚,较大的壁厚可能引起铸件中心凝固时补缩不足,增压结束后此区域还没有完全凝固,继续收缩产生缩孔[7~10],模流分析见图4。因此,如何解决铸件缩孔处的补缩不足,也许才是问题的关键。一般来讲,铸件的补缩时通过料饼→浇道→内浇口→铸件这条路径进行的。由于铸件厚大部位后于内浇口凝固,切断了增压后期的补缩通道,因此无法补缩。
缩孔是铝合金压铸件常见的内部缺陷,常出现在产品壁厚较大或者易形成热点的位置。一般来讲,只要缩孔不影响产品的使用性能,都以合格的方式来判定。然而,对于一些重要部位,如汽车发动机汽缸体的冷却水道孔或润滑油道孔,出现缩孔是不允许判定合格的。
某企业的一款铝合金制发动机曲轴箱,采用布勒28000kN冷室压铸机铸造,材质为ADC12合金,成分见表1。铸件毛坯质量为6.3 kg,后工序进行X射线探伤时发现第二个曲轴轴承孔油道出现缩孔,离油道约8 mm,存在较大的漏油风险。据统计,2017年该位置的缩孔报废率为5%,经过一系列的探索,成功地将废品率降低为0.2%。本课题从铝合金压铸件缩孔的形成机理[1-5]和铸造条件两方面出发,分析铸件产生缩孔的原因,寻求改善措施,以期为日后解决铝合金压铸件缩孔问题提供参考。一、铝合金压铸件缩孔形成机理及形态--缩孔形成机理:导致铝合金压铸件缩孔的原因较多,追溯其本源,主要是铝合金从液相向固相转变过程中铝液补缩不足而导致。常见的缩孔原因有:①模温梯度不合理,导致铝液局部收缩不一致。②铝液浇注量偏少,导致料饼薄,增压阶段补压不足。③模具存在热结或尖锐区域。④模具的内浇口宽度不够,面积较小,导致铸件过早凝固,增压阶段压力传递受阻、铝液无法补缩。⑤铸造压力设置过低,补缩效果较差。图1为铝合金铸件缩孔形成的示意图。铸件缩孔形态:缩孔是一种铝合金压铸件乃至铸件常见的内部缺陷,常出现在产品壁厚较大、模具尖角和模温温差较大等区域。图2为某款发动机曲轴箱缩孔形态,缩孔呈似椭圆状,距离轴承油道孔约10 mm,内壁粗糙,无光泽。缩孔区域铸件壁厚较大,约为22 mm;油道孔销子前端无冷却水,模温较高。汽车发动机曲轴的两大轴颈(主轴颈和连杆轴颈)工作载荷较大,磨损严重,工作时必须进行压力润滑。在此情况下,轴颈的油道孔附近若存在缩孔,将会严重影响润滑效果。二、缩孔相关对策:铝合金压铸件产生铸造缺陷的原因有产品本身的结构特征、模具设计得浇注系统及冷却系统设计不合理、工艺参数设计不合理等原因[1~4]。根据常见的铸造缺陷原因以及铝合金铸件缺陷处理流程,探索解决铝合金压铸件厚大部位缩孔的相应对策。前期分析及对策:铸件缩孔的前期分析从容易操作的工艺参数出发,通过现场测量及观察,测得模具内浇口厚度为4 mm,计算的内浇口速度为40 m/s,产品壁厚*薄处为4.6 mm;料饼厚度为25 mm;铸造压力为60MPa。由经验可知,模具设计符合产品的结构特征,模具浇注系统应该不存在增压阶段补缩不足的问题。但是,增压阶段的铝液补缩与料饼厚度和增压压力有直接的关系,合适的料饼厚度与铸造压力才能形成内部组 织致密的铸件,因此,可以怀疑缩孔是由铸造压力偏低和料饼偏薄而导致的。前期铸件缩孔的对策分为两个:①铸造压力由之前的65MPa提高至90MPa;②料饼厚度有原来的25 mm调整为30 mm。采用上述措施后,经过小批量专流验证,缩孔率由5%减低为4.8%,效果不明显,说明工艺参数不是引起铸件缩孔的主因。中期分析及对策:由于引起铸件缩孔的本质原因是铝液凝固时补缩不足而导致,而模具温度分布不均容易导致铝液凝固顺序不合理,从而补缩不足,因此,中期对策分析主要从确保合理的模具温度入手。由产品3D模型可知,铸件缩孔处壁厚为22.6mm,壁厚较大,容易引起较高的模具温度。铝液凝固时,壁厚较大铸件内部铝液由于温度较高,尚处于液相或者固液混合相,而此时内浇口进行补缩的通道可能已经凝固。这样,在增压阶段铸件无法进行铝液补缩,从而有形成缩孔的可能。为确保合适的模具温度,采用热成像仪测得脱模剂喷涂后模具*高温度为272℃(见图3),高于正常的模具喷涂后温度,其他区域模具温度及其分布整体正常。因此,需要降低缩孔处模温。另外,测得此处冷却水孔底部距离模具型腔表面距离较大为20 mm,因为较大的热传递距离会降低模具的冷却效果,所以需要对冷却水孔进行更改。为降低缩孔处模具温度,主要采取3个方法:①改善模具冷却系统。将缩孔附件的冷却水孔深度加深,由距模具表面20 mm变成12 mm,以此快速带走附近模具热量,降低模温;将所有模具冷却水管与水管统一编号,一一对应,防止模具保全时装错,影响冷却效果[5,6]。②降低浇注温度,由675℃变为645℃。③延长缩孔处模具喷涂时间,由2 s变成3 s。实施上述整改措施后,缩孔区域模具喷涂后温度大幅度降低,约为200℃,属于正常范围。缩孔率有4.8%降低到4%,说明此类措施对缩孔具有一定效果,但不能彻底解决此区域的缩孔问题。后期分析及对策:通过前面两次改善,基本保证压铸模具处于理论上的合理状态,即浇注系统设计合理、冷却系统布置合适,工艺参数设计*优。然而,铸件缩孔率仍有4%之多。铸件缩孔处壁厚为22.6 mm,远大于其他部位的壁厚,较大的壁厚可能引起铸件中心凝固时补缩不足,增压结束后此区域还没有完全凝固,继续收缩产生缩孔[7~10],模流分析见图4。因此,如何解决铸件缩孔处的补缩不足,也许才是问题的关键。一般来讲,铸件的补缩时通过料饼→浇道→内浇口→铸件这条路径进行的。由于铸件厚大部位后于内浇口凝固,切断了增压后期的补缩通道,因此无法补缩。
在江苏省扬州市采购【铝合金型材,结构管厂家批发价】请认准恒永兴金属材料销售
有限公司,品质保证让您买得放心,用得安心,厂家直销,减少中间环节,让您购买到更加实惠、更加可靠的产品。(联系人:李经理-18802286588,QQ:554918566,地址:北辰区双街镇京津路西(北方实业发展有限公司内))。