当前位置:
天津 恒永兴金属材料销售
有限公司 >
贵港本地产品News
铝合金型材高压锅炉管价格实惠
更新时间:2025-04-12 21:02:25 ip归属地:贵港,天气:小雨,温度:19 浏览次数:40 公司名称:天津 恒永兴金属材料销售 有限公司
以下是:铝合金型材高压锅炉管价格实惠的产品参数
产品参数 | |
---|---|
产品价格 | 电议 |
发货期限 | 电议 |
供货总量 | 电议 |
运费说明 | 电议 |
品牌 | 恒永兴 |
规格 | 齐全 |
价格 | 电议 |
以下是:铝合金型材高压锅炉管价格实惠的图文视频
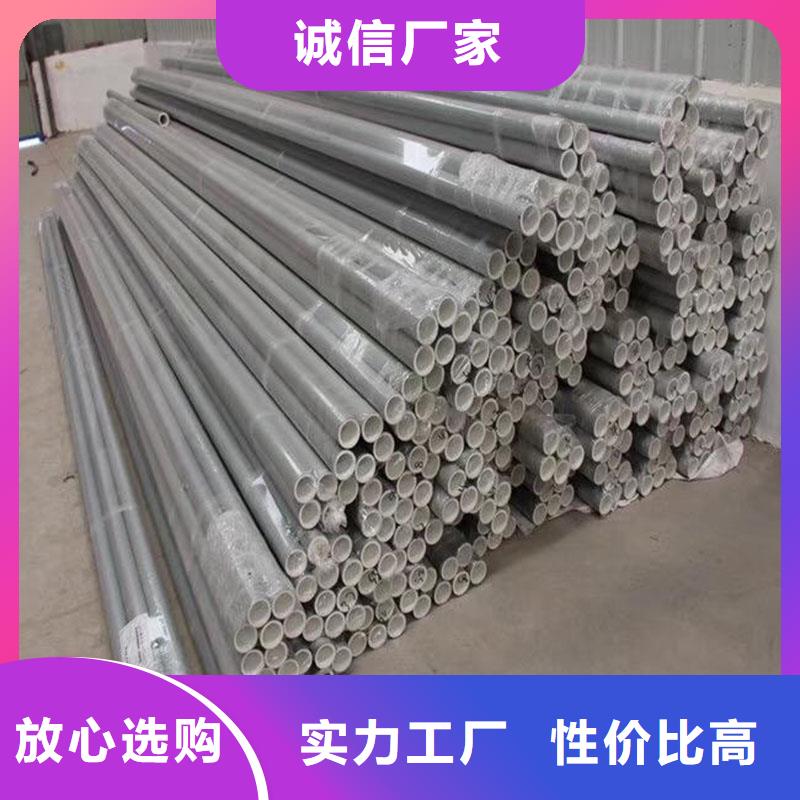

铝合金型材高压锅炉管价格实惠,恒永兴金属材料销售
有限公司为您提供铝合金型材高压锅炉管价格实惠的资讯,联系人:李经理,电话:022-86869388、18802286588,QQ:554918566,发货地:天津北辰区双街镇京津路西(北方实业发展有限公司内)发货到广西省 贵港市 港北区、港南区、覃塘区、平南县、桂平市。 广西壮族自治区,贵港市 贵港市,古称贵州、贵县,别称荷城,位于中华人民共和国广西壮族自治区东南部,广西壮族自治区辖地级市,西江流域中游,浔郁平原中部,是珠江—西江经济带重要节点城市,大西南出海通道的重要门户,中缅油气管道天然气管道终点。贵港港为中国西部地区内河大港,智慧城市试点城市,西江黄金水道流经市境。东临梧州、南临玉林和钦州、西接南宁、北邻来宾。总面积10602平方千米。截至2022年末,贵港市常住人口435.56万人。
无论您是初次接触还是已经熟悉,我们的铝合金型材高压锅炉管价格实惠产品视频将为您带来全新的视觉体验,让您对产品有更深入的了解。
以下是:铝合金型材高压锅炉管价格实惠的图文介绍
铝合金元素分析,各种元素各尽其能---铜元素:铝铜合金富铝部分548时,铜在铝中的zui大溶解度为5.65%,温度降到302时,铜的溶解度为0.45%。铜是重要的合金元素(铝合金元素分析),有一定的固溶强化效果,此外时效析出的CuAl2有着明显的时效强化效果。铝合金中铜含量通常在2.5%~5%,铜含量在4%~6.8%时强化效果zui好,所以大部分硬铝合金的含铜量处于这范围。铝铜合金中可以含有较少的硅、镁、锰、铬、锌、铁等元素。硅元素:Al—Si合金系富铝部分在共晶温度577时,硅在固溶体中的zui大溶解度为1.65%。尽管溶解度随温度降低而减少,介这类合金一般是不能热处理强化的。铝硅合金具有极好的铸造性能和抗蚀性。若镁和硅同时加入铝中形成铝镁硅系合金,强化相为MgSi。镁和硅的质量比为1.73:1。设计Al-Mg-Si系合金成分时,基体上按此比例配置镁和硅的含量。有的Al-Mg-Si合金,为了提高强度,加入适量的铜,同时加入适量的铬以抵消铜对抗蚀性的不利影响。Al-Mg2Si合金系合金平衡相图富铝部分Mg2Si在铝中的zui大溶解度为1.85%,且随温度的降低而减速小。变形铝合金中,硅单独加入铝中只限于焊接材料,硅加入铝中亦有一定的强化作用。镁元素:Al-Mg合金系平衡相图富铝部分尽管溶解度曲线表明,镁在铝中的溶解度随温度下降而大大地变小,但是在大部分工业用变形铝合金中,镁的含量均小于6%,而硅含量也低,这类合金是不能热处理强化的,但是可焊性良好,抗蚀性也好,并有中等强度铝合金元素分析。镁对铝的强化是明显的,每增加1%镁,抗拉强度大约升高瞻远34MPa。如果加入1%以下的锰,可能补充强化作用。因此加锰后可降低镁含量,同时可降低热裂倾向,另外锰还可以使Mg5Al8化合物均匀沉淀,改善抗蚀性和焊接性能。锰元素:Al-Mn合金系平平衡相图部分在共晶温度658时,锰在固溶体中的zui大溶解度为1.82%。合金强度随溶解度增加不断增加,锰含量为0.8%时,延伸率达zui大值。Al-Mn合金是非时效硬化合金,即不可热处理强化。锌元素:Al-Zn合金系平衡相图富铝部分275时锌在铝中的溶解度为31.6%,而在125时其溶解度则下降到5.6%铝合金元素分析。锌单独加入铝中,在变形条件下对铝合金强度的提高十分有限,同时存在应力腐蚀开裂、倾向,因而限制了它的应用。在铝中同时加入锌和镁,形成强化相Mg/Zn2,对合金产生明显的强化作用。Mg/Zn2含量从0.5%提高到12%时,可明显增加抗拉强度和屈服强度。镁的含量超过形成Mg/Zn2相所需超硬铝合金中,锌和镁的比例控制在2.7左右时,应力腐蚀开裂抗力zui大。
铝灰的化学成分由于原料组成及工艺等不同,具有较明显的差异性,主要由金属铝、氧化铝及盐熔剂等的混合物构成。具体是:Al10%~30%,Al?O320%~40%,Si,Mg,Fe氧化物7%~15%,K,Na,Ca,Mg氯化物和少量氟化物15%~30%。其中部分氧化物和氯化物附着于金属铝的表面。耐火材料属资源型产业,化学成分及类型多种多样,具有容纳各种原材料的空间。铝灰的化学成分与耐火材料的主要原料铝矾土相近,可以考虑直接或经加工处理后成为耐火原料,为铝灰的有效利用开辟一条新途径,既保护环境,又降低耐火材料企业的生产成本,对企业可持续发展具有一定帮助。铝灰加入耐火材料配料中的应用:1.1作为防爆剂:能改善不定形耐火材料衬体的透气性,防止衬体在烘烤过程中由于产生的蒸气压过大而发生爆 裂的物质称为防爆剂,也称为快干剂(可快速烘烤的添加剂)。不定形耐火材料的防爆剂有活性金属铝粉,铝粉与H?O反应生成Al(OH)?,并放出H?,在浇注料尚未凝固前,H?从浇注料逸出时会形成毛细排气孔,从而提高其排气性。王立旺[1]采用铝灰替代铝粉作防爆剂,用于铁沟浇注料,其铝灰的化学成分是:Al31.63%,Al?O?18.15%,AlN9.25%,MgO6.16%,SiO?12.21%,Fe?O?7.27%,CaO2.23%,Na?O2.15%,K?O1.03%,TiO?2.04%,Cr?O?0.58%,其他7.33%。其中的Al,AlN能水化放出气体。试验得出铁沟浇注料中加入w(铝灰)4%,能很好地起到防爆作用,铝灰加入过多,会出现鼓胀开裂,铝灰还能促进铁沟料硬化,缩短施工时间。1.2加入高炉出铁口炮泥中:黄朝晖等人发明在高炉出铁口炮泥中添加铝灰0.4%~40%替代铝质和硅质原料。其他原料是:工业级刚玉、碳化硅、中温沥青颗粒粉、苏州土细粉、焦炭粉等,以焦油及改性沥青和酚醛树脂为结合剂,混合搅拌均匀,过真空练泥机挤出后,即得到炮泥。其性能稳定,能满足生产要求,并能降低生产成本。1.3代替煅烧铝矾土:有人研究在浇注料、预制件和耐火粘土制品中加入铝灰取代煅烧的铝矾土,而铝灰无需煅烧,可直接作原料,大约用量在5%。利用铝灰加工配制耐火材料,众所周知,原料是耐火材料的基础,高质量的耐火原料才能生产好的产品。对耐火原料基本要求就是耐火性能,即耐火度1580℃以上的原材料才能作为耐火原料。铝灰中除了Al?O?以外,还含有较多耐火性能较低的杂质成分,因此,一般不能用铝灰直接配制耐火材料,需要进一步加工处理,除去杂质,提高Al?O?含量,才能考虑用作耐火材料。以下就铝灰加工处理方法作简要介绍。2.1铝灰的浮选法提纯:刘瑞琼等采用油酸钠为捕收剂,当pH值固定在8.6左右,捕收剂用量为1000g/t时,浮选后铝灰w(Al?O?)含量由原来43.14%提高到86.41%,回收率68.89%。可以替代铝矾土冶炼氧化铝基电熔材料。2.2制取α-Al?O?:α-Al?O?是刚玉等高级耐火材料的主要原料。用铝灰提取的基本原理是:在400~600℃的温度下,铝灰中的金属铝、氧化铝与NaOH和NaNO?反应生成可溶于水的金属盐,并用水将其溶出,实现铝与其他杂质分离之后,使用晶种分解法处理含铝溶液,*终得到α-Al?O?。得出的制备条件是:碱灰比(mNaOH/m铝灰)1.3,盐灰比(mNaNO?/m铝灰)0.7,按比例要求配合,混合均匀,在500℃下熔炼,熔炼时间60min;用去离子水在60℃恒温水溶中浸出熔炼产物,浸出时间30min,固液比1∶4,铝浸出率*高达92.71%,浸出后抽滤,固液分离,浸出液经过净化,调整苛性比,晶种分解和煅烧获得氧化铝。谢刚等人采用加压碱浸、波活化辅助的方法回收铝灰中氧化铝。首先将铝灰破碎、筛分、水洗,与NaOH溶液按固液比1∶7混合搅拌均匀,然后在高压釜内,于140℃,1.15MPa反应6h,经进一步固液分离、酸中和、水洗分离后,将产物置于输出功率5W/g的波设备干燥活化7min,抽风速度为30m/min,*终可得Al?O?产品。还有人通过王水浸取法及添加氧化钇制备高硬度γ-Al?O?。首先铝灰在室温下溶解在王水中,然后在pH为9~10的条件下沉淀,加入0~20%氧化钇粒子,经压实后于1550~1650℃煅烧可得高硬度γ-Al?O?。2.3制取纳米氧化铝:在刚玉耐火制品中引入α-Al?O?粉,降低烧结温度,节约能源,提高其性能。例如:在用电熔刚玉(Al?O?99.5%)的配料中,加入4%~8%的α-Al?O?粉和1%~2%的α-Al?O?纳米粉,制品的烧成温度由1700~1800℃降至1400℃。刘晓红等采用硫酸浸取铝灰制备纳米氧化铝的工艺方法是:首先在80℃搅拌条件下,用硫酸溶液多次浸取铝灰中的铝离子,经过滤分离得到硫酸铝溶液,然后将碳酸氢铵溶液加入到硫酸铝溶液中,在40℃条件下搅拌反应60min,生成前驱体碳酸铝铵沉淀和硫酸铵溶液,经陈化,真空抽滤分离,硫酸铝铵沉淀洗涤干燥后于1200℃煅烧1h,得到粒径约70nm的α-Al?O?粉。2.4利用铝灰冶炼棕刚玉:耐火材料用棕刚玉一般是用特级铝矾土冶炼而成,Al?O?含量94.5%~97%,是中、耐火材料的主要原料,尤其不定形耐火材料用量较多。近年来,为了节能环保,降低生产成本,有人在研究用铝灰冶炼棕刚玉,其中刘瑞琼等[5]试验的低温冶炼制备棕刚玉的效果较好。其生产过程是:将1份铝灰(小于0.10mm)放入2~5份90~100℃热水中,浸泡6~10h,将水排出,并加入排出等质量的90~100℃热水浸泡2~14h,浸泡为放热反应,不断搅拌,保持水温90~100℃,确保铝灰不沉积,将浸泡后的铝灰分离出来后用流动水漂洗,漂洗水流为3~6m/min,然后用真空过滤机过滤,再经80~110℃烘干至水分低于20%,即完成预处理。在电弧炉中熔炼:在铝灰中加入0.5%~4%的沉淀剂铁屑,在炉中1700~1800℃冶炼6~8h,熔融还原铝灰中的SiO?,Fe?O?,TiO?等氧化物,冷却后经粉碎,磁选和筛分得到棕刚玉产品。其试用的铝灰及棕刚玉产品的化学成分见表2。2.5合成Sialon粉:Sialon陶瓷是20世纪70年代后迅速发展起来的一类高温结构材料,Sialon材料以优越的力学性能、热学性能和化学稳定性,被认为是*有希望的高温陶瓷材料之一。Sialon为Si?N4-AlN-Al2O?-SiO?系固溶体,采用纯化学原料制备,成本高。李家镜等[6]采用铝灰、炭黑和粉煤灰为原料,用碳热铝热复合还原氮化工艺制备Sialon粉体。试用铝灰及粉煤灰的化学成分如表3。称好料,进行球磨12h(用Si?N4球,无水乙醇为介质),然后进行干燥、过筛、压成圆片,再进行煅烧,自然冷却后磨成粉,研究了原料组成、合成温度对生成物相的影响。结果表明:在原料中当Si/Al为1(铝灰为33%,粉煤灰为50%)时,加入17%炭黑,合成温度1450℃,得到的主要物相为Si?Al?O?N(5β-Sialon,Z=3)和SiAl4O?N(415R)的产物;在Si/Al为1.5时,加入80%粉煤灰,1450℃可制备较纯的Si?Al?O?N5粉。2.6制备镁铝尖晶石:镁铝尖晶石是重要的耐火原料,以它为颗粒,镁砂为细粉,制备与刚玉配制钢包用浇注料。李晓娜[7]以铝灰、铝矾土和电熔镁砂为原料,铁屑为沉淀剂,焦炭为还原剂,采用高温电熔法合成富铝镁铝尖晶石。试验表明:加入铝灰20%,40%,60%生产的镁铝尖晶石,其综合指标超过铝矾土基镁铝尖晶石的技术指标;加入40%铝灰时,综合指标*好,其含Al?O?82.48%,SiO?0.35%,MgO14.10%,CaO1.12%,Fe?O?0.5%(质量分数)显气孔率0.9%,体积密度3.48g/cm3,耐火度>1800℃;铝灰加入40%,60%生产的尖晶石中含有六铝酸钙(CA6)相。2.7制备TiN-Al?O?复相耐火原料:TiN-Al?O?复合材料具有优异的高温稳定性,耐磨性及力学性能,是一种优异的耐火材料。刘海涛等[8]以金红石和铝灰为原料,以铝灰中的金属铝为还原剂,采用铝热还原氮化法合成TiN-Al?O?复合粉体。试验用铝灰及金红石的化学成分见表4。其原理是:根据反应式6TiO?+8Al+3N?=6TiN+4Al?O?计算铝灰和金红石理论质量比为16∶27。具体做法是:先称好料,放入球磨机中,干磨12h,以40MPa压力,干压成型坯体,然后放入石墨坩埚,在流动氨气中,600~1400℃,保温5h煅烧。在1300℃煅烧的产品按理论用量合成的产物主要是TiN,α-Al?O?,少量倍长石和MgAl?O4。经计算,TiN为30.4%,α-Al?O?为45.8%,随铝灰增加α-Al?O?增多,TiN减少,当铝灰过量50%时,TiN为26.4%,α-Al?O?为55.0%。TiN-Al?O?复合材料的抗折强度达520.2MPa。2.8电熔莫来石:陈海等[9]利用铝灰电熔莫来石。具体步骤是: 步是铝灰预处理过程,首先在1100℃下煅烧铝灰,使金属铝部分转变为Al?O?,然后将煅烧的铝灰放入水槽中,加入盐酸进行清洗,然后烘干;第二步是电熔,按铝灰、铝矾土与硅石的质量分数比为:30%~80%:0~50%:10%~20%的范围内,混合均匀后加入电弧炉中,熔炼,倒出,冷却,破粉碎,分选,得到莫来石。利用铝灰制取耐火材料结合剂3.1合成聚合氯化铝:聚合氯化铝又称碱式氯化铝,简称PAC,是介于AlCe?和Al(OH)?之间的水解产物,其化学通式为(Al(2OH)nCe6-n)m,其中m<10,n=1~5。聚合氯化铝分为固体和液体两种,固体通常为黄色或无色的树脂状产品,Al?O?含量40%~50%;液体呈无色,黄褐色或黑色,Al?O?含量10%以上。聚合氯化铝可作为定型耐火制品、耐火可塑料、捣打料和浇注料结合剂,对碱化度和密度有一定要求,一般要求碱化度为46%~72%,密度为1.17~1.23g/cm3。谢英惠等[10]研究以铝灰为原料制取聚合氯化铝。其中中和法是将烧碱和盐酸分别与铝灰反应,产生铝酸钠和三氯化铝,然后以合适的配比合成聚合氯化铝。而酸溶法是将铝灰和盐酸反应一次直接产出液体聚合氯化铝。具体操作是:用水洗法除去水溶解的盐类,处理后铝灰Al?O?含量30%左右,然后将工业盐酸与一定量水放入反应器内,搅拌并用水浴加热,称取铝灰逐步加入盐酸溶液中,反应放热,反应温度96℃,时间6~12h,反应结束加入一定水稀释物料,试验认为,铝灰∶HCe∶水为3∶1∶3,反应6~8h为宜,调节pH值为3.5~4.5,陈化15~24h,得到液体聚合氯化铝产品。3.2制取硫酸铝:将硫酸铝溶于水中,可作为定型和不定型耐火材料的结合剂。由于硫酸铝溶液呈酸性,因此主要用于酸性和中性耐火材料结合剂。康文通等[11]研究的以铝灰为原料制备硫酸铝的工艺流程是:铝灰—加入硫酸和水进行反应—过滤除去滤饼—滤液除去杂质—浓缩—冷却结晶—硫酸铝产品。其中反应时间3h,硫酸浓度30%,硫酸用量1.05(以硫酸实际用量与理论用量之比表示),pH值为3,收率达93.2%
随着我国 广西贵港工字钢市场经济的发展,恒永兴金属材料销售 有限公司着力加强企业文化建设,提出了“双赢靠诚信”的经营理念,“立足创新、专注质量、诚信服务、真诚合作、共同发展”是我们始终如一的追求,为客户提供质优、、可靠的产品是我们永恒的方针,“审时慎思,明辨力行”打造优越的 广西贵港工字钢。我们将不断超越自我,一如既往的为客户创造价值!
浅谈如何提高铝型材用粉末涂料的耐候性:喷涂在铝型材表面的粉末涂膜的耐候性,是影响铝型材寿命的关键性因素。本文主要从粉末涂料的原材料、配方结构、制作工艺、固化条件等技术角度分析,并结合所做的实验结果,总结出几个提高粉末涂料耐候性的可供参考的思路,从而*终达到延长铝型材寿命的目的。随着国民经济的快速发展,粉末涂料的户外应用越来越普遍,人们对粉末涂层耐候性和耐久性的关注度不断提高,特别是对铝型材、天花板、幕墙板等室外用品表面的粉末涂膜的耐候性要求越来越高。粉末涂料主要由树脂、固化剂、助剂、颜填料等组成,喷涂在铝型材表面的涂层随着时间的延长,受周围自然因素如日晒、雨淋、氧化、冷热变化以及生物等的作用,会出现性能逐渐降低的现象,即老化。粉末涂料抑制或延缓自然老化的能力称为耐自然老化性,简称耐老化性,也叫耐候性。影响粉末涂料耐候性的因素很多,其中包括粉末涂料成分中的树脂、固化剂、颜填料、助剂等各种原材料的性能、用量、配比等内部因素;以及粉末涂料制作过程的工艺条件和涂料的固化程度;还有涂膜的使用环境如日光(主要是紫外线)的作用、大气的组成(氧、臭氧、工业烟雾等)、湿度(包括酸雨、盐雾等)、温度变化等外部因素。
从粉末涂料本身的角度来看,提高粉末涂层耐候性能主要从原材料、配方结构以及制作工艺等方面着手。一、原材料:粉末涂料主要由树脂、固化剂、助剂、颜填料等材料组成,这些原材料的耐候性,基本上决定了涂料的耐候性。因此,要提高粉末涂料的耐候性能,首先要选择耐候性能满足铝型材行业要求的原材料,而且这些耐候性合格的原材料也要满足涂膜的其他性能。当涂膜的各项性能相互间产生冲突时,可以根据客户的要求侧重于某项性能,但是人工加速老化试验结果要满足GB 5237.4-2008中加速耐候性的要求。1.树脂:因为树脂是粉末涂料的主要成膜物质,是决定粉末涂料性质和涂膜性能的*主要成分,所以树脂的选择至关重要。选取市面上大型厂家常用的铝型材用粉末涂料聚酯树脂,使用同一配方结构和相同制作工艺分别制粉进行300小时耐老化试验以及涂膜外观比较,结果如表1所示。(加速老化条件为8小时光照,4小时凝露循环;UVB-313EL灯,辐照度0.65W/㎡,光照温度60℃;凝露温度50℃)由试验结果可知,树脂D、F、H在通一系列的树脂中耐候性较好,但这种树脂的缺点是分子量大,熔融黏度高,如果应用在平面粉中*终会导致涂膜流平性能差。所以,通过在粉末涂料配方中选用耐候性能好的树脂来提高平面粉的耐候性能时,必须考虑到涂膜的流平是否会变差,变差之后客户能否接受。2.固化剂:尽管HAA体系的固化剂环保型众所周知,但是它的缺点是固化反应有副产物形成,厚喷时容易产生针孔、猪毛孔等弊端,涂膜过烘烤耐泛黄性和耐久性不如TGIC体系。[1]铝型材行业目前难以接受HAA体系的这些弊端,或者说是大部分粉末厂家没有解决这些弊端,所以铝型材用粉末涂料还是以TGIC体系为主。固化剂TGIC对粉末涂料的耐候性能也有一定的影响。
经过对国内三家销售量排名靠前的厂家的TGIC进行耐老化检测,发现它们的耐老化性能基本一致,无较大的差别。因此,在通过固化剂TGIC的选择上去提高粉末涂料的耐候性,并无多大的意义。3.颜料:颜料对粉末涂料耐候性的影响在原材料中是除了树脂之外影响*大的因素,因为颜料在使用过程中会褪色,所以对于铝型材用粉末涂料的颜料的选择也很重要。市场上即使是用一种颜色的颜料,它的品种非常多,不同品种的色相、着色力、遮盖力、耐候性、耐热性等性能千差万别,这给我们粉末涂料厂家的选择带来很大的难度。颜料按化学组成分为无机颜料和有机颜料,它们的优缺点如表2所示。颜料的选择要从多方面考虑,如颜料的色相、着色力、遮盖力、耐热性、耐候耐光性、耐沸水性、毒性等等;而且由于一些颜料可能带有对树脂和固化剂起到促进作用的活性基团,所以也要考虑颜料对涂料反应速度、粘度的影响。为了提高粉末涂料的耐候性,颜料要选择耐光性在7-8级(8级*好),耐候性4-5级(5级*好)的品种,同时耐热性和耐沸水性要满足铝型材行业的使用要求。从表2可知,由颜料本身的性质决定,有机颜料的耐光性和耐候性有限,而无机颜料不够鲜艳,所以一些鲜艳颜色的粉末大多使用了耐光性和耐候性有限的有机鲜艳颜料,这就是鲜艳颜色的涂膜耐老化色差较大的主要原因。因此,为了保证鲜艳颜色涂膜的耐候性,除了选用耐候性能优异的其他材料,更加要注意颜料的选择。4.填料:填料的重要功能是添加到粉末涂料中以后,能够改进涂膜的硬度、刚性和耐划伤性等物理力学性能,同时有利于改进粉末涂料的贮存稳定性、松散性和带电等性能。[3]铝型材粉末涂料中*常用的填料为硫酸钡,经过对多个厂家的硫酸钡进行耐老化检测,发现耐候性能无明显差别。因此,为了保证涂料的耐候性,必须使用纯度高的硫酸钡作为填料。硫酸钡进仓前必须经过检验,使用10%的盐酸溶液是*简单快捷的方法,可以快速检测出硫酸是否含有碳酸钙,碳酸钙会降低涂料的耐候性能,不能作为铝型材用粉末涂料的填料。5.助剂:在粉末涂料配方中,助剂的用量很少,但在一般粉末涂料配方组成中是不可缺少的成分,而且对涂膜的外观及某些性能起决定性作用。经过对各国内大型厂家同类助剂进行加速老化对比试验后,发现不同厂家的流平剂、光亮剂、安息香等对涂膜耐老化性能影响不大;而不同厂家的蜡粉、消光剂对涂膜耐老化的影响较大。因此,为了提高粉末涂料的耐候性,可以考虑使用耐老化性能好的蜡粉和消光剂。二、配方结构:通过粉末涂料中聚酯树脂的酸值和固化剂羟基当量的计算,设计合适的固化剂用量,并通过加速老化试验的验证,使用*佳的固化剂用量,使涂料在固化时能够充分固化,从而达到*好的耐候性能。
在满足粉末涂料各项性能的前提下,尽量在配方中减少原材料的种类,特别是对涂膜耐候性起负作用的材料。在不影响涂膜遮盖力以及硬度、耐磨性的前提下,适当降低配方中的颜料(特别是吸油量大的颜料)和填料的用量,使配方中的颜料能够在熔融混炼过程充分被树脂包覆,在涂膜的使用过程中减少颜料的颜色变化,从而达到提高涂膜耐候性的目的。三、制作工艺:粉末涂料制作过程主要包括预混合、熔融挤出、压片破碎、分级粉碎四个阶段,其中预混合、熔融挤出两个工艺对粉末涂料的耐候性能有很大影响。预混合的作用是为了使粉末涂料配方中的各种原材料组成分散均匀,为熔融挤出打下良好的基础。为了提高耐候性,在预混合阶段,原材料必须按一定的先后顺序进行投料,而且投料量控制在混料缸容量的20%-80%,并适当延长混合时间。熔融挤出是为了使粉末涂料组成中的各种成分混合均匀,也就是达到粉末涂料成品中的每个粒子组成成分一样。为了提高耐候性,在熔融挤出阶段,在不出现胶化粒子的前提下,适当提高挤出机温度(特别是在气温较低的情况下),使树脂熔融成一种流体,保证颜料能有良好的润湿和获得*大的剪切力,有利于颜料等的高度分散,使各组分成为一个均匀的体系;在保证生产进度的同时,可以适当降低挤出速度,保证物料有充足的熔融混炼时间;从而提高混炼效果,使粉末涂料中的颜料填料被树脂充分包覆,而且各种原材料成分粒子分散均匀,特别是固化剂和树脂能按配方的比例混炼均匀,固化时涂膜能够充分固化,从而增加涂膜的表面致密性,*终提高粉末涂层的耐候性。四、固化条件:粉末涂料只有充分固化的情况下,树脂的高分子链才会和固化剂完全交联,各项物理化学性能才会达到*佳状态,耐候性能也不例外。因此,提高耐候性能必须使粉末涂料充分固化,固化时要控制好温度和时间。综上所述,对于提高铝型材用粉末涂料的耐候性,可参考如下思路:选用耐候性能好且流平不至于太差的树脂;注意鲜艳颜料、蜡粉、消光剂的选择;设计有利于提高涂膜耐候性的配方结构;控制好粉末涂料生产工艺。
从粉末涂料本身的角度来看,提高粉末涂层耐候性能主要从原材料、配方结构以及制作工艺等方面着手。一、原材料:粉末涂料主要由树脂、固化剂、助剂、颜填料等材料组成,这些原材料的耐候性,基本上决定了涂料的耐候性。因此,要提高粉末涂料的耐候性能,首先要选择耐候性能满足铝型材行业要求的原材料,而且这些耐候性合格的原材料也要满足涂膜的其他性能。当涂膜的各项性能相互间产生冲突时,可以根据客户的要求侧重于某项性能,但是人工加速老化试验结果要满足GB 5237.4-2008中加速耐候性的要求。1.树脂:因为树脂是粉末涂料的主要成膜物质,是决定粉末涂料性质和涂膜性能的*主要成分,所以树脂的选择至关重要。选取市面上大型厂家常用的铝型材用粉末涂料聚酯树脂,使用同一配方结构和相同制作工艺分别制粉进行300小时耐老化试验以及涂膜外观比较,结果如表1所示。(加速老化条件为8小时光照,4小时凝露循环;UVB-313EL灯,辐照度0.65W/㎡,光照温度60℃;凝露温度50℃)由试验结果可知,树脂D、F、H在通一系列的树脂中耐候性较好,但这种树脂的缺点是分子量大,熔融黏度高,如果应用在平面粉中*终会导致涂膜流平性能差。所以,通过在粉末涂料配方中选用耐候性能好的树脂来提高平面粉的耐候性能时,必须考虑到涂膜的流平是否会变差,变差之后客户能否接受。2.固化剂:尽管HAA体系的固化剂环保型众所周知,但是它的缺点是固化反应有副产物形成,厚喷时容易产生针孔、猪毛孔等弊端,涂膜过烘烤耐泛黄性和耐久性不如TGIC体系。[1]铝型材行业目前难以接受HAA体系的这些弊端,或者说是大部分粉末厂家没有解决这些弊端,所以铝型材用粉末涂料还是以TGIC体系为主。固化剂TGIC对粉末涂料的耐候性能也有一定的影响。
经过对国内三家销售量排名靠前的厂家的TGIC进行耐老化检测,发现它们的耐老化性能基本一致,无较大的差别。因此,在通过固化剂TGIC的选择上去提高粉末涂料的耐候性,并无多大的意义。3.颜料:颜料对粉末涂料耐候性的影响在原材料中是除了树脂之外影响*大的因素,因为颜料在使用过程中会褪色,所以对于铝型材用粉末涂料的颜料的选择也很重要。市场上即使是用一种颜色的颜料,它的品种非常多,不同品种的色相、着色力、遮盖力、耐候性、耐热性等性能千差万别,这给我们粉末涂料厂家的选择带来很大的难度。颜料按化学组成分为无机颜料和有机颜料,它们的优缺点如表2所示。颜料的选择要从多方面考虑,如颜料的色相、着色力、遮盖力、耐热性、耐候耐光性、耐沸水性、毒性等等;而且由于一些颜料可能带有对树脂和固化剂起到促进作用的活性基团,所以也要考虑颜料对涂料反应速度、粘度的影响。为了提高粉末涂料的耐候性,颜料要选择耐光性在7-8级(8级*好),耐候性4-5级(5级*好)的品种,同时耐热性和耐沸水性要满足铝型材行业的使用要求。从表2可知,由颜料本身的性质决定,有机颜料的耐光性和耐候性有限,而无机颜料不够鲜艳,所以一些鲜艳颜色的粉末大多使用了耐光性和耐候性有限的有机鲜艳颜料,这就是鲜艳颜色的涂膜耐老化色差较大的主要原因。因此,为了保证鲜艳颜色涂膜的耐候性,除了选用耐候性能优异的其他材料,更加要注意颜料的选择。4.填料:填料的重要功能是添加到粉末涂料中以后,能够改进涂膜的硬度、刚性和耐划伤性等物理力学性能,同时有利于改进粉末涂料的贮存稳定性、松散性和带电等性能。[3]铝型材粉末涂料中*常用的填料为硫酸钡,经过对多个厂家的硫酸钡进行耐老化检测,发现耐候性能无明显差别。因此,为了保证涂料的耐候性,必须使用纯度高的硫酸钡作为填料。硫酸钡进仓前必须经过检验,使用10%的盐酸溶液是*简单快捷的方法,可以快速检测出硫酸是否含有碳酸钙,碳酸钙会降低涂料的耐候性能,不能作为铝型材用粉末涂料的填料。5.助剂:在粉末涂料配方中,助剂的用量很少,但在一般粉末涂料配方组成中是不可缺少的成分,而且对涂膜的外观及某些性能起决定性作用。经过对各国内大型厂家同类助剂进行加速老化对比试验后,发现不同厂家的流平剂、光亮剂、安息香等对涂膜耐老化性能影响不大;而不同厂家的蜡粉、消光剂对涂膜耐老化的影响较大。因此,为了提高粉末涂料的耐候性,可以考虑使用耐老化性能好的蜡粉和消光剂。二、配方结构:通过粉末涂料中聚酯树脂的酸值和固化剂羟基当量的计算,设计合适的固化剂用量,并通过加速老化试验的验证,使用*佳的固化剂用量,使涂料在固化时能够充分固化,从而达到*好的耐候性能。
在满足粉末涂料各项性能的前提下,尽量在配方中减少原材料的种类,特别是对涂膜耐候性起负作用的材料。在不影响涂膜遮盖力以及硬度、耐磨性的前提下,适当降低配方中的颜料(特别是吸油量大的颜料)和填料的用量,使配方中的颜料能够在熔融混炼过程充分被树脂包覆,在涂膜的使用过程中减少颜料的颜色变化,从而达到提高涂膜耐候性的目的。三、制作工艺:粉末涂料制作过程主要包括预混合、熔融挤出、压片破碎、分级粉碎四个阶段,其中预混合、熔融挤出两个工艺对粉末涂料的耐候性能有很大影响。预混合的作用是为了使粉末涂料配方中的各种原材料组成分散均匀,为熔融挤出打下良好的基础。为了提高耐候性,在预混合阶段,原材料必须按一定的先后顺序进行投料,而且投料量控制在混料缸容量的20%-80%,并适当延长混合时间。熔融挤出是为了使粉末涂料组成中的各种成分混合均匀,也就是达到粉末涂料成品中的每个粒子组成成分一样。为了提高耐候性,在熔融挤出阶段,在不出现胶化粒子的前提下,适当提高挤出机温度(特别是在气温较低的情况下),使树脂熔融成一种流体,保证颜料能有良好的润湿和获得*大的剪切力,有利于颜料等的高度分散,使各组分成为一个均匀的体系;在保证生产进度的同时,可以适当降低挤出速度,保证物料有充足的熔融混炼时间;从而提高混炼效果,使粉末涂料中的颜料填料被树脂充分包覆,而且各种原材料成分粒子分散均匀,特别是固化剂和树脂能按配方的比例混炼均匀,固化时涂膜能够充分固化,从而增加涂膜的表面致密性,*终提高粉末涂层的耐候性。四、固化条件:粉末涂料只有充分固化的情况下,树脂的高分子链才会和固化剂完全交联,各项物理化学性能才会达到*佳状态,耐候性能也不例外。因此,提高耐候性能必须使粉末涂料充分固化,固化时要控制好温度和时间。综上所述,对于提高铝型材用粉末涂料的耐候性,可参考如下思路:选用耐候性能好且流平不至于太差的树脂;注意鲜艳颜料、蜡粉、消光剂的选择;设计有利于提高涂膜耐候性的配方结构;控制好粉末涂料生产工艺。
说到船用铝板,大家*熟悉的要数5083铝板了。船用铝板是铝板产品研发应用的新兴领域,目前船板的生产能力已成为衡量铝板厂家综合实业的重要指标。那么,船舶制造厂家为何如此青睐5083铝板?5083铝板属于Al-Mg系合金,中等强度,具有耐蚀性好、焊接性优良、冷加工性较好的优势,广泛用于制造飞机油箱、油管、交通车辆、船舶钣金件、仪表、街灯支架、铆钉、五金制品、电器外壳等。在船舶制造领域,多采用5083H116/H321/H112状态的铝板,应用于船舶甲板、发动机台座、船侧、船底外板等部位。5083铝板满足船用铝板的选材要求:1、较高的比强度和比模量。船舶的结构强度和尺寸与材料的屈服强度和弹性模量密切相关,由于铝合金的弹性模量和密度大体相同,合金元素的添加也影响甚,因此在一定范围内提高屈服强度对减轻舰船结构有力。5083铝板属于中等强度,能同时具备优良的耐蚀性和可焊接性。2、焊接性优良。5083铝板具有良好的焊接抗裂性,在焊接时不容易出现裂纹现象。3、耐蚀性优良。耐蚀性能是船用合金的主要标志之一,5083铝板是典型的防锈铝板,耐腐性好,能适应恶劣的海洋环境,经久耐用。4、密度小。铝合金比重小,能减轻船板重量,节省能耗,增加载重。5、环保。铝合金不燃烧,遇火,而且回收利用率高,可循环再利用,环保性好。
通过温度控制提高挤压铝型材产量,通常,如果没有非预定的停机时间,那么*大产量主要决定于挤压速度,而后者受制于四个因素,其中三个固定不变而另一个则是可变的。 个因素是挤压机的挤压力,挤压力大的可在锭坯温度较低时顺利地挤压;第二个因素是模具设计,挤压时金属与模壁的摩擦通常可使通过的铝合金的温度上升35~62℃;第三个因素是被挤压合金的特性,是限制挤压速度的不可控制的因素,型材的出口温度一般不可超过540℃,否则,材料表面质量会下降,模痕明显加重,甚至出现粘铝、凹印、裂缝、撕裂等。*后一个因素是温度及其受控程度。如果铝型材挤压机的挤压力不够大,很难顺利挤压或甚至出现塞模现象而挤不动时,就可提高锭坯温度,但挤压速度应低些,以防材料的出口温度过高。每一个合金都有其特定的*优的挤压(锭坯)温度。生产实践证明,锭坯温度*好保持在430℃左右(挤压速度≥16mm/s时)。6063合金型材的出模温度不得超过500℃,6005合金的*高出口温度为512℃,6061合金的*好不大于525℃。出模温度的不大变化也会影响产品的产量与质量。挤压筒温度也是很重要的,特别应注意预热阶段的温度升高,应避免各层之间产生过大的热应力,*好是使挤压筒与衬套同时升高到工作温度。预热升温速度不得大于38℃/h。*好的预热规范是:升高到235℃,保温8h,继续升温到430℃,保温4h后,才投入工作。这样不但能保证内外温度均匀一致,而且有足够的时间一切内部热应力。当然在炉内加热挤压筒是*佳的预热方式。在挤压过程中,挤压筒温度应比锭坯温度低15~40℃。如果挤压速度过快,以致挤压筒温度上升到高于锭坯温度,就要设法使挤压筒温度下降,这不但是一件麻烦的工作,而且产量会下降。在生产速度上升过程中,有时受电偶控制的加热元件会被切断,可是挤压筒温度仍在上升。如果挤压筒温度高于470℃,挤压废品就会上升。应根据不同的合金确定理想的挤压筒温度。千万不要认为预热挤压筒是在浪费时间、消耗能源。某工厂为赶生产任务,一方面用内部电阻元件加热,另一方面又以液化气烧嘴加热。在这种情况,温度无法测量与控制,会产生巨大的热应力,内衬温度高,膨胀比外套的快,以致挤压筒裂开,并听到“炸裂”的声音。挤压轴在工作过程中会积蓄内应力,这种应力大到一定程度会产生疲劳裂纹,一旦受到非轴向的径向力作用就会断裂。因此,挤压轴的累计工作时间达到4500h后,*好进行一次应力处理,在430~480℃保温12h,然后随炉冷却到50℃以下。遗憾的是,我国很少有工厂照此处理。
生产优质表面建筑型材时,对挤压垫温度也应严格控制,以减少表面色调不一致废品量。固定挤压垫的质量比活动的好得多,能积聚更多的热量,因而能降低锭坯端头温度,能减少杂质进入型材内,有助于提高产量。美国卡斯图尔公司(Castool)采用压缩空气冷却挤压垫与挤压轴,使其温度降到50℃左右。模具温度对于获得高的产量起着重要的作用,一般不得低于430℃;另方面,也不得过高,否则,不但硬度可能下降,同时会产生氧化,主要在工作带。在模具加热过程中,应避免模具之间紧靠着,阻碍空气流通。*好采用带格的箱式加热炉,每个模放于一个单独的箱内。锭坯在挤压过程中的温度升高可达40℃左右或更高些,升高量主要决定于模具设计。为了获得*大产量,对各项温度决不可忽视,应记录各个温度并严加控制,以找出机台的*大产量与各项温度的关系。然后,铝型材挤压生产厂的员工都应牢记:温度的精密控制,对提高产量是至关重要的。
通过温度控制提高挤压铝型材产量,通常,如果没有非预定的停机时间,那么*大产量主要决定于挤压速度,而后者受制于四个因素,其中三个固定不变而另一个则是可变的。 个因素是挤压机的挤压力,挤压力大的可在锭坯温度较低时顺利地挤压;第二个因素是模具设计,挤压时金属与模壁的摩擦通常可使通过的铝合金的温度上升35~62℃;第三个因素是被挤压合金的特性,是限制挤压速度的不可控制的因素,型材的出口温度一般不可超过540℃,否则,材料表面质量会下降,模痕明显加重,甚至出现粘铝、凹印、裂缝、撕裂等。*后一个因素是温度及其受控程度。如果铝型材挤压机的挤压力不够大,很难顺利挤压或甚至出现塞模现象而挤不动时,就可提高锭坯温度,但挤压速度应低些,以防材料的出口温度过高。每一个合金都有其特定的*优的挤压(锭坯)温度。生产实践证明,锭坯温度*好保持在430℃左右(挤压速度≥16mm/s时)。6063合金型材的出模温度不得超过500℃,6005合金的*高出口温度为512℃,6061合金的*好不大于525℃。出模温度的不大变化也会影响产品的产量与质量。挤压筒温度也是很重要的,特别应注意预热阶段的温度升高,应避免各层之间产生过大的热应力,*好是使挤压筒与衬套同时升高到工作温度。预热升温速度不得大于38℃/h。*好的预热规范是:升高到235℃,保温8h,继续升温到430℃,保温4h后,才投入工作。这样不但能保证内外温度均匀一致,而且有足够的时间一切内部热应力。当然在炉内加热挤压筒是*佳的预热方式。在挤压过程中,挤压筒温度应比锭坯温度低15~40℃。如果挤压速度过快,以致挤压筒温度上升到高于锭坯温度,就要设法使挤压筒温度下降,这不但是一件麻烦的工作,而且产量会下降。在生产速度上升过程中,有时受电偶控制的加热元件会被切断,可是挤压筒温度仍在上升。如果挤压筒温度高于470℃,挤压废品就会上升。应根据不同的合金确定理想的挤压筒温度。千万不要认为预热挤压筒是在浪费时间、消耗能源。某工厂为赶生产任务,一方面用内部电阻元件加热,另一方面又以液化气烧嘴加热。在这种情况,温度无法测量与控制,会产生巨大的热应力,内衬温度高,膨胀比外套的快,以致挤压筒裂开,并听到“炸裂”的声音。挤压轴在工作过程中会积蓄内应力,这种应力大到一定程度会产生疲劳裂纹,一旦受到非轴向的径向力作用就会断裂。因此,挤压轴的累计工作时间达到4500h后,*好进行一次应力处理,在430~480℃保温12h,然后随炉冷却到50℃以下。遗憾的是,我国很少有工厂照此处理。
生产优质表面建筑型材时,对挤压垫温度也应严格控制,以减少表面色调不一致废品量。固定挤压垫的质量比活动的好得多,能积聚更多的热量,因而能降低锭坯端头温度,能减少杂质进入型材内,有助于提高产量。美国卡斯图尔公司(Castool)采用压缩空气冷却挤压垫与挤压轴,使其温度降到50℃左右。模具温度对于获得高的产量起着重要的作用,一般不得低于430℃;另方面,也不得过高,否则,不但硬度可能下降,同时会产生氧化,主要在工作带。在模具加热过程中,应避免模具之间紧靠着,阻碍空气流通。*好采用带格的箱式加热炉,每个模放于一个单独的箱内。锭坯在挤压过程中的温度升高可达40℃左右或更高些,升高量主要决定于模具设计。为了获得*大产量,对各项温度决不可忽视,应记录各个温度并严加控制,以找出机台的*大产量与各项温度的关系。然后,铝型材挤压生产厂的员工都应牢记:温度的精密控制,对提高产量是至关重要的。
铝合金型材高压锅炉管价格实惠,恒永兴金属材料销售
有限公司专业从事铝合金型材高压锅炉管价格实惠,联系人:李经理,电话:022-86869388、18802286588,QQ:554918566,发货地:北辰区双街镇京津路西(北方实业发展有限公司内),以下是铝合金型材高压锅炉管价格实惠的详细页面。